Your New Gas Compressor is Installed. Do THIS Before it Goes Online
by Randy Franiel, Senior Accounts Manager, Canada
Shaking forces are an inherent part of the operation of reciprocating natural gas compressors. As we’ve explored in previous blogs, understanding and managing the causes of these shaking forces is a key design consideration. This is because excessive shaking or vibration due to unbalanced forces and pulsation is directly associated with mechanical failure.
Intuitively, that’s pretty easy to understand. If you’re driving a car and your wheels are out of balance, the car will be shaking and bumping along as you drive. The faster you go, the greater the vibration will be. Depending how fast you’re going, how much you’re shaking and how long this goes on, sooner or later the wheel bearings or something else will fail.
I also like to compare a recip compressor to a tuning fork. Unbalanced forces, the twisting and shaking of the compressor, and pulsation (because it’s sending pulses of gas down the pipeline), all excite that tuning fork. If the forces are significant, over time, the equipment will break.
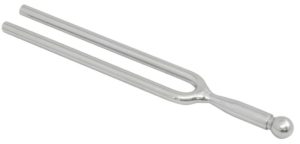
Because recip compressors have inherent forces, we’re not aiming for vibration-free operation, but rather to be able to control these forces. Going in, based on the design, you need to know how and at what frequency a given compressor’s forces act. Pulsation within these parameters is expected and acceptable in our industry
Because a compressor is built in a shop but operated in the field, however, you won’t fully understand why and how it vibrates based on its design and manufacturing alone. That’s why I recommend that producers do a vibration survey after they receive a compressor.
The survey measures vibration in three planes: x, y and z, throughout your compressor package. It gives you a comprehensive understanding of what’s vibrating, why and how much. The survey examines the compressor, the compressor valves, piping, clamps, vessels, coolers and how the equipment is braced and bracketed. Back to the tuning fork analogy, the survey allows you to understand the mechanical resonance of that compressor while it’s operating.
For the most part, the way the compressor forces will already be known and reflected through the design process. Sometimes, though, it’s not until a piece of equipment is in the field running that you see everything.
If a compressor is moving around in a way that’s outside the design, that needs to be investigated right away. Sometimes it’s as simple as a plate that’s not holding adequately, which you can remedy very easily. Without the insight provided by the vibration survey, you might not find this issue until there’s a breakdown.
Vibration assessment is done through on-site inspection by trained personnel, but newer technology can also play a role. In my next post, which will be the last in this series, I’ll explore a real-world example of the value of vibration assessment in maximizing compressor performance.
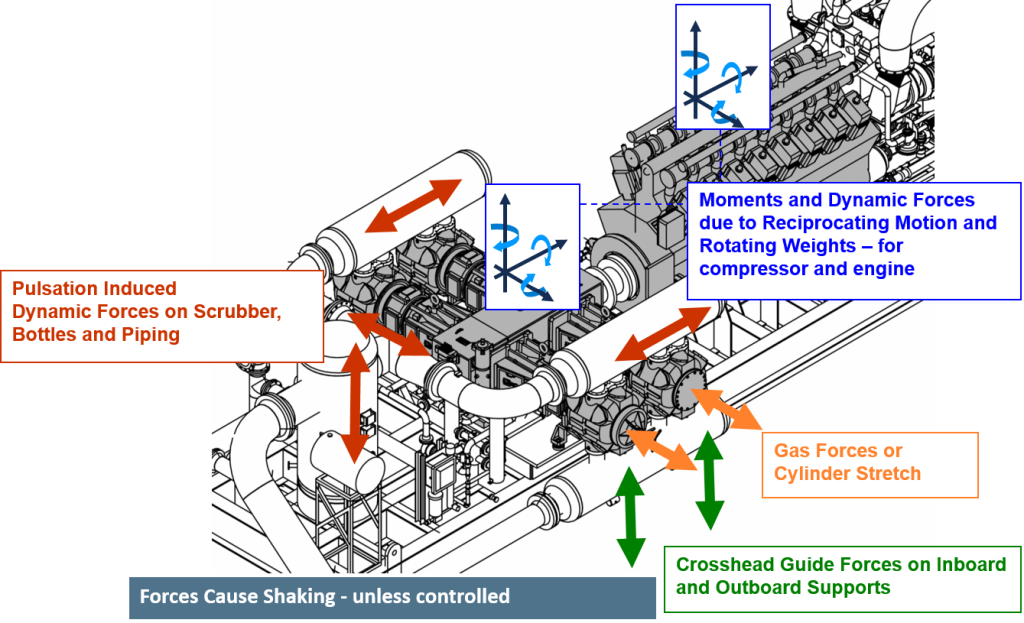
If you have questions about reciprocating compressors or gas compression,
please contact Randy Franiel by email or phone: 1-855-262-2487
Email Us
What you Need to Know About Reciprocating Gas Compressors
Have you read all the articles in our blog series?
Intro: What You Need to Know about Reciprocating Gas Compressors
Part 1: How a Fundamental Design Flaw Robs Your Profits
Part 2: Understanding the Importance of Shaking Forces
Part 3: Volumetric Efficiency: Why it Matters and How to Maximize It
Part 4: An Approach to Compressor Selection, and the #1 Issue to Watch For
Part 5: Your New Gas Compressor is Installed. Do THIS Before it Goes Online
Part 6: When Gas Compressors Operate Outside Design, Communication is Key