Compression Equipment Optimization
When a compression package is newly engineered, built and commissioned, it should do precisely what the gas producer needs it to do. Over time, however, the nature of the gas and the performance of the package can both change.
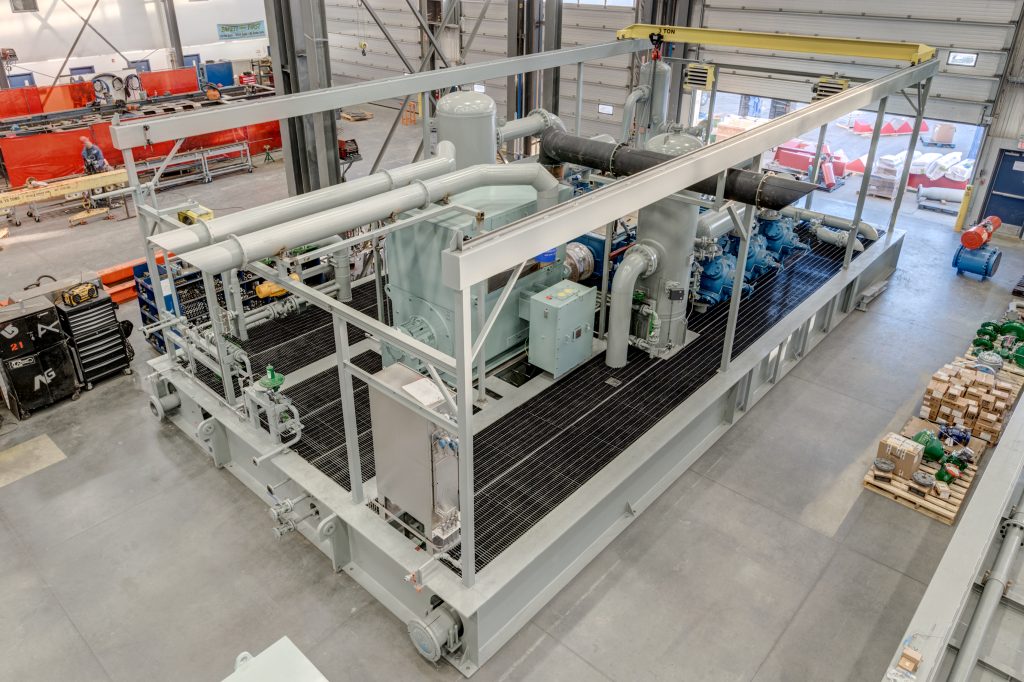
When that happens, a gap opens up between what you have and what you need. The longer this goes on, the more production and profitability can suffer.
This is why Kirk Dunn, Compass’ Parts + Service Manager, recommends that producers make equipment optimization a regular event. Equipment optimization – think of it as midway between a routine service and a full-scale overhaul – can typically boost production efficiency between 3% and 10%, or up to 20% in extreme cases.
“The customer might see a decline in gas flow and call us,” says Dunn. “Efficiency could also be acceptable, but they’d just like to get a little more out of their equipment.”
The vast majority of Compass equipment optimizations take place in the field, which allows the producer to minimize downtime. Dunn’s Service Team is highly experienced, with expertise in a wide range of equipment set-ups. That’s crucial, because diagnosing the problem isn’t always easy. The process begins with a detailed collection of the operating parameters of the equipment.
“Sometimes equipment is worn out, and components need to be replaced with new ones, or tuned up,” he says. “It can be as little as, the engine isn’t tuned up correctly. Sometimes the unit was mis-designed for the gas you’re working with, or operating conditions have changed since the unit went in.”
Like so much at Compass, equipment optimization relies on individual skill, teamwork and smooth communication. If a minor adjustment is called for, the on-site mechanic sends data back to the product support team, which evaluates the unit’s performance and sends the technician detailed instructions for how to make the adjustments. If a component needs to be replaced, Compass’ Engineering group will design this change and schedule implementation with the Service Team.
As Dunn sees it, achieving even a 3% boost to production efficiency makes equipment optimization a sound investment. As equipment performance or gas conditions change, optimization can align what you have with what you need, and extend the life of your equipment.
“Even small gaps in performance can become significant to the producer very quickly,” says Dunn. “We recommend looking at an equipment optimization service every six to 12 months. If a customer ever has questions, of course, we’re always here to help.”